How maritime companies get more uptime with conditional and predictive maintenance
This article explores the significance of conditional and predictive maintenance in the maritime industry. We also show you how edge intelligence can significantly increase the efficiency of those types of maintenance strategies.
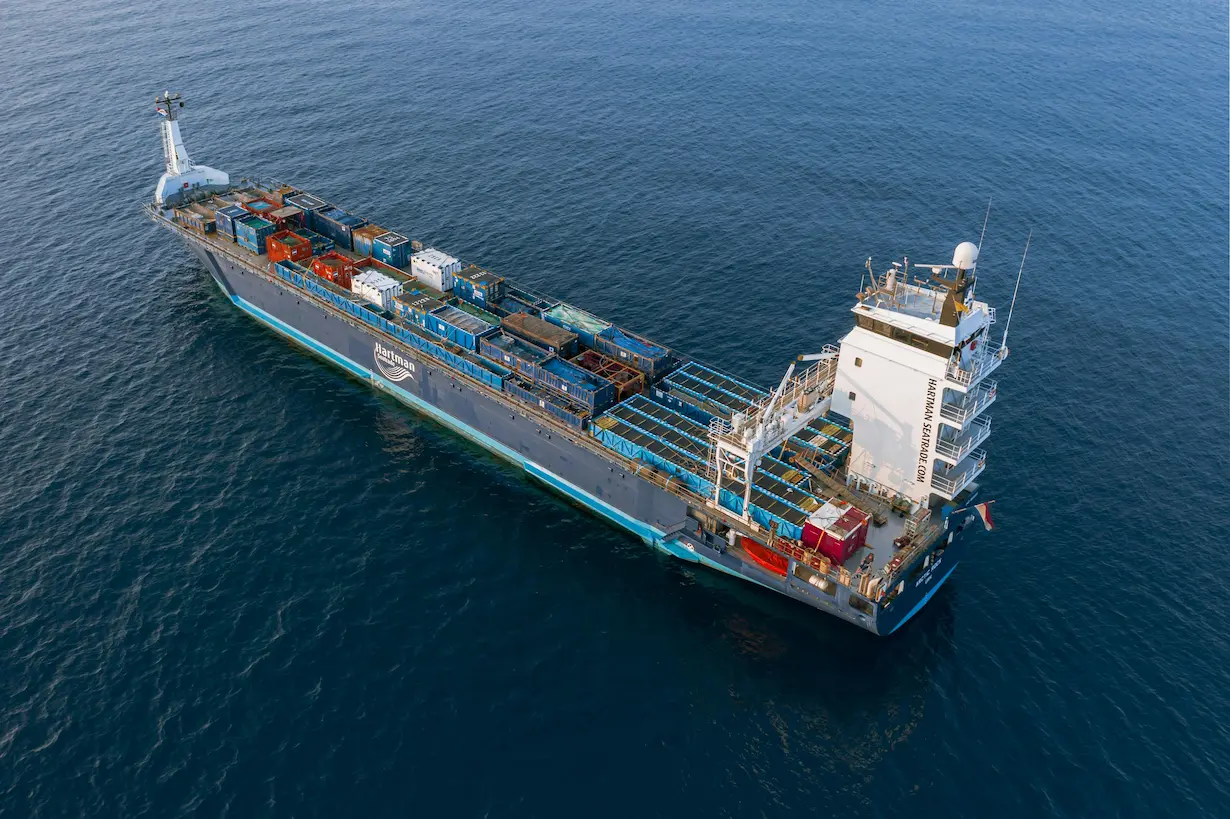
Imagine a massive cargo ship stranded in the middle of the ocean due to an unexpected engine failure. The crew faces delays and safety risks, and your company has to deal with the financial losses. This nightmare scenario underscores the critical importance of maintaining vessel uptime.
This article explores the significance of conditional and predictive maintenance in the maritime industry. We also show you how edge intelligence can significantly increase the efficiency of those types of maintenance strategies.
Why preventing maritime vessel downtime is crucial for success
First of all, a quick clarification on the specific topic of this article. When we talk about businesses operating in the maritime industry, we’re not talking about your average boutique fishing company or tour operator with a ship or two. We’re talking big-time industry here.
Maritime organizations operating large fleets are the types of businesses that stand to gain – or lose – the most from managing maintenance and uptime efficiently.
And there’s much to be gained here. A 2018 study on predictive maintenance shows that 93% of companies consider their maintenance processes not to be very efficient.
On top of that, in industrial maintenance, we see that 80% of companies link using a computerized maintenance management system (CMMS) to greater productivity. With most of these companies indicating predictive maintenance is the best strategy to reduce downtime and reduce the probability of failure.
Maritime companies, specifically, are often hired by third parties for a variety of projects like:
- Maintaining coastlines
- Installing ocean-based wind parks
- Transporting cargo from point A to B
- Laying internet cables in the ocean
- Transporting specialized cargo (e.g. oil, coal, etc.)
These companies’ maritime vessels operate somewhere in the middle of the ocean, or other typically remote areas. Any equipment breakdown can cause downtime in operations. Downtime can potentially delay the completion of the project you’re hired for.
Delays, in turn, can result in contractual penalties and affect your bottom line. Some machinery breakdown can even prove fatal if it causes crew accidents or irreparable damage to capital-intensive equipment.
On top of this, downtime of a ship also means downtime for a crew, often consisting of highly paid professionals.
This is why a preventive maintenance strategy is crucial for success in the maritime industry.
How maintenance stands in the way of uninterrupted vessel operations
The role of maintenance in this type of industrial maritime operations, then, is simple. Maintenance is inevitable and it leads to more delays and higher costs. If anything major breaks on an offshore vessel, the cost of repair will be astronomical.
Repairs might entail sending a member of your onshore team with the right expertise to the vessel, for instance. Apart from the delay in repair time, you’re also looking at the additional costs involved in flying the maintenance crew to the offshore vessel.
The difference between predictive and conditional maintenance
The difference between predictive and conditional maintenance isn’t so much a clear difference. It’s more that one is the means to the other. Basically condition monitoring is the means to predictive maintenance.
If the condition of your capital-intensive industrial assets is monitored properly (using the right sensor data), this allows you to implement the right maintenance cycle for your equipment. This, in turn, leads to preventive maintenance, eliminating unnecessary delays and additional costs.
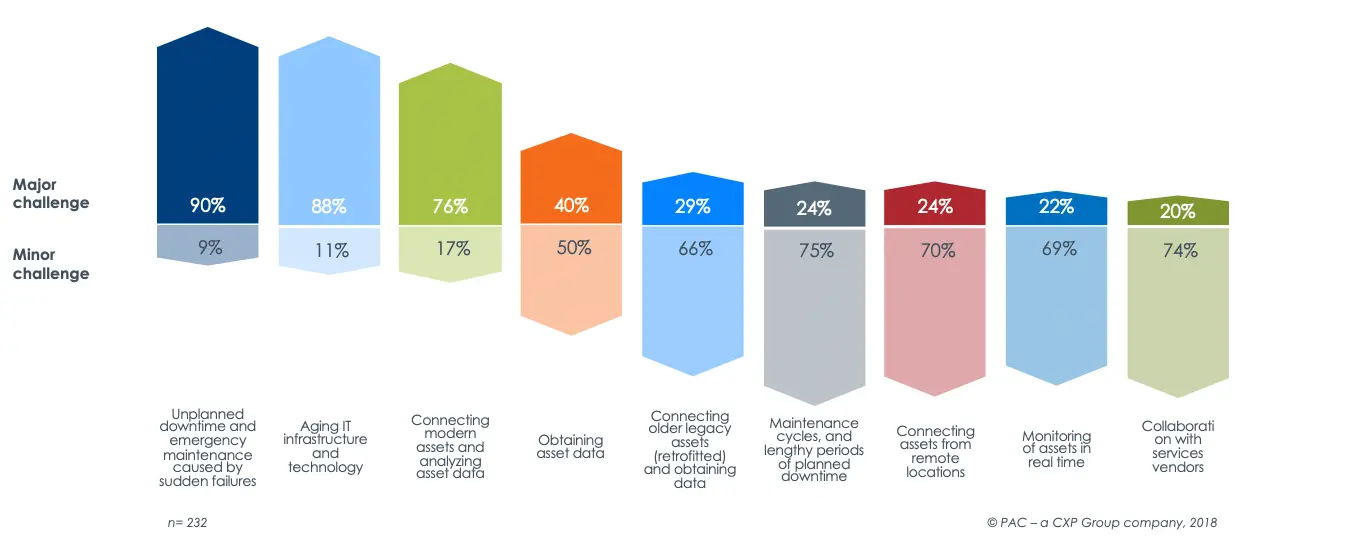
Industries that typically use condition-based maintenance
As for specific industries that tend to invest more in condition-based and predictive maintenance, we’re looking at industries like:
- Manufacturing
- Maritime
- Renewable energy & PV / solar
Industrial companies in general see a tangible ROI from investing in predictive maintenance. Some industrial companies report metrics such as 2-6% increased availability, 10-40% reduction in reactive maintenance and 5-10% inventory cost reduction.
Important to note: in order to scale predictive maintenance strategies, industrial partners need to work with partners like Helin that can create test cases to demonstrate tangible business value before iterating on those solutions. But more on that later. First, let’s look at how to get started.
Getting started with conditional and predictive maintenance
Condition-based monitoring of equipment builds the foundation for a strong predictive maintenance strategy. These maintenance strategies are also cost-effective because they ensure you never act prematurely and do too much (which is expensive) not do too little (leading to equipment failure).
As a matter of fact, researchers found 30% of maintenance activities are carried out too frequently and as much as half of every dollar spent on predictive maintenance is wasted. Condition-based monitoring can help alleviate this problem.
As for getting started, the first thing you need to do is establish a baseline, which means distinguishing a pattern of data illustrating the normal state of your equipment. This allows you to start monitoring deviation from that baseline.
In order to do so, you’ll need to start capturing high-frequency data in real-time as a best practice for baseline establishment.
Most onboard vessel equipment already includes sensors and typically provides a point-solution for accessing sensor data. Start out by monitoring this data in real-time, instead of on a weekly or monthly basis.
Complications may arise when you have multiple point solutions each housing their own sensor data. In a fragmented situation like this, it’s challenging to unify all the data necessary to get actionable insights into your performance and maintenance needs.
How edge computing makes conditional and predictive maintenance more effective
When you’re managing a large-scale maritime operation, the challenges and complications of fragmented sensor data put you at an alarming risk of facing costly downtime. One way to circumvent these challenges is through edge computing.
In short, edge computing is a distributed IT architecture in which client data is processed locally, at the periphery of the network, i.e. at the site of each individual maritime asset. Edge computing significantly enhances predictive maintenance capabilities.
With edge computing, you capture high frequency, real-time data from sensors on onboard equipment. This real-time data provides accurate insight into the actual health of the equipment allowing both onboard and offshore teams to monitor and plan for the maintenance activities.

This proactive approach ensures continuous and safe operations of the vessel. When applied across an entire fleet, the benefits are amplified manifold. Using edge computing simply makes your conditional monitoring and predictive maintenance way more effective.
At Helin, we take it one step further by offering you the means to ingest sensor data in any format or protocol, making it completely hardware agnostic. Regardless of your hardware, Helin can handle all types of data formats, helping maritime companies to develop robust and effective data and predictive maintenance strategies, with more uptime and a better bottom line as a direct result.
P.s. if you want to read up on how this would work in action, here’s a case study on how Helin helped Boskalis lift existing data infrastructure to a secure edge computing ecosystem.
Get started with Helin’s industrial edge intelligence platform today
Are you looking to get more uptime out of your maritime vessels through conditional monitoring and predictive maintenance, but don't know where to start? Consider Helin’s industrial edge intelligence platform.
We’d be happy to show you exactly what Helin edge computing can mean for your maintenance strategies, vessel uptime and productivity. Want to learn more? Make sure to get in touch for a demo of the Helin platform.
Want to read more?
Stay up to date with the latest trends and developments on the topic of industrial edge computing, monitoring and intelligence.
Get real-time insights
into your remote assets
Combine local artificial intelligence with a centrally managed data infrastructure for more accuracy, reduced congestion on your network and lower costs.

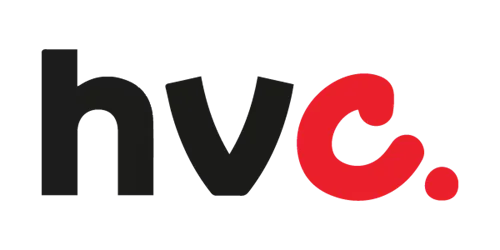
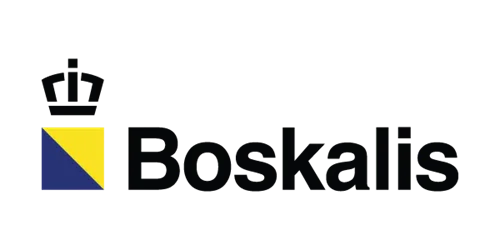